Lying about 120 km north of Fendt’s Bavarian headquarters, its factory is located in Asbach-Bäumenheim, with a sister plant in Marktoberdorf in the Allgäu region. The factory is one of the world’s most advanced facilities. CABs and bonnets are built from scratch on-site at the former and then transported on a just-in-time basis to the latter for mounting on the tractors, a stage of the production line referred to as ‘the marriage’.
From parts production plant to the main transmission line, to preparatory work on the main assembly line, all played a key role in the landmark achievement of the 20 000th.
The 20 000th Fendt produced in late December 2022 happened to be a 724
The Fendt 700 Vario has been one of the most popular tractor series in South Africa. It combines strength, agility, functionality and comfort thanks to the new driver’s workstation and integrated FendtONE platform. It is a versatile tractor and the perfect partner for all kinds of work, from easy-going grassland work to dynamic transport and heavy-duty field or fleet operations.
The tried and proven six-cylinder engine on the Fendt 700 Vario delivers 144 hp to 237 hp with a top speed of 50 km/h. With a 6.1 litre cubic capacity, four valves per cylinder and common rail injections, the engine delivers a high torque driving experience. It is a compact high-horsepower tractor designed for maximum performance and load capacity, while the engine and transmission are perfectly in tune for high overall efficiency.
The Vario gearbox provides a stepless drive from 0.02 km/h to a maximum speed of 50 km/h, with the continuously variable speed adjustment optimising engine use. A Tractor Management System (TMS) controls the engine and transmission to ensure they are always working at their economical best.
Features like automatic maximum output control reduce fuel consumption even further, with the engine always running in the ideal speed range. The maximum load control feature sets how far the engine speed is allowed to drop under load before the transmission shifts according to the engine load or to the target speed if the TMS or cruise control is engaged.
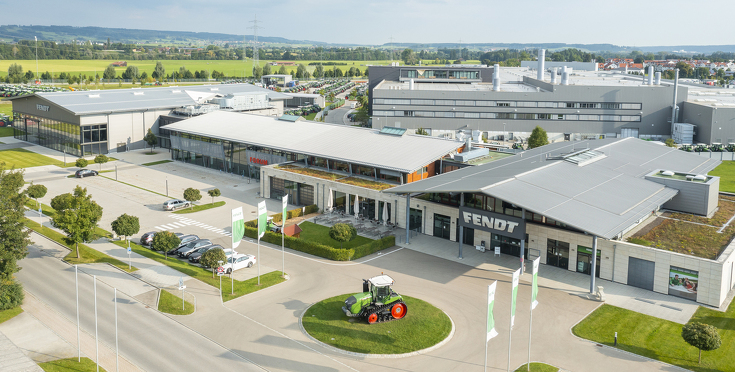
How Fendt achieved 20 000 units in 2022
The tractors are manufactured in huge workshops at the headquarters of Germany’s biggest producer of agricultural machinery. Various models are manufactured on just one production line. The heart of every tractor is the engine and transmission block.
The engine frame is mounted on the transmission at the front. Here the relatively large element is the fan unit, followed by the front axle and hydraulic tank. Over the next three hours the units pass through 29 assembly stations.
Then the world’s most powerful series tractor is ready. First the data cables are fitted to the engine and transmission block. The hi-tech tractor contains many kilometres of cabling and sensors that constantly monitor what the tractor is doing at any given moment. All this information is relayed during operation to a central computer in the CAB.
After this station, the tractor is fitted with its air and particle filter, catalytic converter and fuel tank. All components are supplied from an on-site logistics warehouse for the respective model at precisely the right time.
At the next station, the driver’s cab is positioned on the engine block, which is manufactured and preassembled at another factory. All the fitters are specialists who have completed 3.5 years training as farm equipment or car mechanics or mechatronics technician.
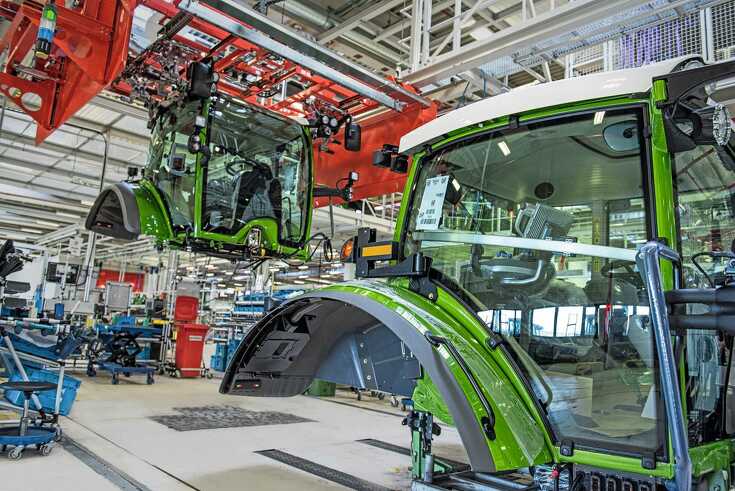
The CAB is secured by huge bolts. For the tough demands of operating in the field, it must be mounted securely. This important work step is known as the ‘marriage’. In the automotive industry it refers to installing the engine in the vehicle, while with tractor assembly it means linking the CAB to the tractor.
In the next assembly section, the fitters install the battery case and then hook up the electrics. The engine bonnet is attached next, followed by the radiator hoods. At the next station the tractor receives its diesel and hydraulic oil and cooling water.
A series of tests is carried out to ensure that the indicators and headlights function correctly and that the windscreen wiper works. The steering system and onboard electronics are checked. After the software has been downloaded, the various electronic functions on the tractor are tested. The axles are adjusted and checked. The new tractor must pass more than 100 tests before it is allowed to leave the factory.
During assembly, the tractor goes through seven quality control checks, including the transmission, hydraulic and electrical systems. Only once the tractor passes all the tests is it released for the next assembly phase. If an error or defect is detected, the tractor is taken to the rework section to be repaired and checked once again by specially trained staff.
The next work step is one of the most important: Fitting the wheels. It is precision assembly, with laser guided electric forklifts transporting the wheels straight to the tractor, which is jacked up 12 cm. Later the wheels are secured by huge wheel nuts.
Now the tractor can move for the first time under its own power. A roller test rig is used to show what it can do for the first time and whether all the work on the vehicle has been carried out properly. The tractor gets the green light after the engine and brakes functions are tested. It is now complete and ready for the final assembly.
Workstations and processes to ensure safety and quality
All workstations and processes are cutting edge, with customer focus part and parcel of the overall production and assembly with a special focus on quality which Fendt is world famous for. Fendt benchmarks its production with the latest generation processing centres and hi-tech CNC machines, including laser-cutting machines. With the most up-to-date paint shop system globally for tractor body painting, Fendt sets new milestones in the agricultural technology industry.
In Asbach-Bäumenheim, production begins with raw material delivered to the factory in the form of tubes, profiles and metal sheets. The single-piece production system is based on state-of-the-art technology and hi-tech systems such as flatbed or five-axis lasers for exceptional quality and unique design.
The CAB and bonnet components are worked precisely in the first step, with complex contours cut out of raw material plates using a 2D laser-cutting system. The distinctive and unique form of the Fendt tractors, defined mainly by the cab and hood, is achieved with 3D cutting in ultra-modern laser centres. The technology in both these 2D and 3D cutting systems guarantees meticulous component processing.
State-of-the-art welding technologies and processes are used such as innovative welding robots. With these modern methods, Fendt can produce unique cabs such as the VisioPlus with its curved front window for the new 700 Vario series.
The wheel assembly is a technical highlight. The wheels are delivered in the sequence of production, pre-sorted on special supports. Laser-navigated electric forklifts pick up the wheels and drive them automatically to where they are needed. Here the tractor body is raised by up to 600 mm for ergonomic, semi-automated wheel assembly.
What does this mean for the South African farmer?
Fendt leading the way in terms of technology and quality adds tremendous value to South African farmers due to the extremely economic fuel consumption and world-leading technology. Further value is added by Fendt enabling precision planting, spreading and spraying, all coupled with a driving and operating experience unmatched by any competitor. This all starts where the tractors are designed and manufactured. This is why Fendt is investing so much money, time and skill development to ensure that when a customer buys a Fendt it meets their expected standard in terms of quality and assurance.