Lincolnshire Field Products (LFP) farms approximately 6,700ha of which most is for vegetable and root crop production, and 1,800ha is cereals. Combinable crops include peas, wheat, beans and oilseed rape. The wheat is mainly for feed, and some is for seed and almost all the straw is baled and used to cover carrots or sold for energy production and cattle bedding.
Local AGCO dealer Chandlers (Farm Equipment) Ltd has supplied the farm with machinery for more than 30 years and works closely with the LFP team. The tractor fleet is mainly Fendt, but there are Massey Fergusons too which are also supplied by the dealer. Since 2002, Challenger tracked tractors have been used, and the farm’s experienced operators were consulted during development of the Fendt Vario MT tracked models which replaced AGCO’s Challenger brand. “Fendt tractors are reliable, efficient and have excellent ergonomics which is important to our full-time operators,” explained LFP Senior Farm Manager Paul Langford. “They also hold their value well.”
Two Fendt Ideal 8T combines with 10.5m SuperFlow headers have completed their second harvest for Lincolnshire Field Products.
The combines were chosen for their output, grain quality and gentle handling of straw, and also for the back-up from local dealer Chandlers.
High output
With such a large area of combinable crops to harvest, high work rates are essential to make the most of suitable weather windows. “Chandlers couldn’t offer combines with the output needed, so we have owned a succession of different brands over the years as we tried to find the ideal machine,” said Paul. “In 2009 we bought our first rotary combine, which was replaced by another brand after five years. Although both gave us the capacity we wanted, the rotary separation was aggressive and straw quality suffered. When we heard that Fendt’s Ideal was in development we were immediately interested and as we learned more about its design we could see it was something special and would give us the performance we needed.”
“When we were discussing replacement of the farm’s previous combines - efficiency and increased output to reduce harvesting hours were key factors, and also the new combines had to be on tracks,” added Chandlers Fendt Product Specialist, Clive Barber. “With the Fendt Ideal we had a machine which ticked all the boxes.”
Two Ideal 8T combines with 10.5m SuperFlow headers were ordered to replace two 9.0m machines in time for the 2019 harvest. “Our priority was to achieve a high forward speed without incurring losses, and we very much liked the design of the Ideal with its efficient drive arrangement, simple crop processing concept and predicted fuel economy. As it was the first year of general availability we expected teething problems, but were confident that if issues occurred we would be well looked after by Fendt and the Chandlers team,” added Paul.
The farm chose Fendt Ideal 8T combines with 10.5m headers rather than the larger Ideal 9T with a wider header to suit its trailers and smaller fields.
The Ideal 8 is the mid-size model in the range, powered by a 538hp MAN engine and with a Dual Helix threshing system with twin 4.84m long rotors and a 12,500-litre grain tank. The larger Ideal 9 with a wider header was considered, but Paul said the Ideal 8 is better matched to the farm’s large fleet of trailers which are also used for other crops, and there are many small fields for which the 10.5m header is better suited. “I’m not sure we would have gained anything, and as we do a lot of road work between working areas the shorter header is also easier to move around."
Tracks were specified to protect the land which ranges from grade 1 silt to heavy clay, and almost all of it can suffer from compaction. They are also preferred to tyres for road use and allow 40kph transport speeds.
User-friendly automation
Ben Walker is the main combine operator. He first drove combines in 2000 on another local farm but moved to LFP in 2002 where his father was farm manager at the time and has driven the combines every harvest since. His Ideal is equipped with IDEALharvest – which uses a network of acoustic sensors along the rotor and cleaning shoe to monitor crop movement and display the capacity status of the threshing and cleaning system, including losses, in real time. A grain quality camera records images of the clean grain elevator which are scanned by the system for cracked or broken grains and sample purity, with results displayed on the in-cab screen. IDEALharvest uses data from the acoustic sensors and the camera to adjust the combine’s systems automatically to achieve a sample quality or loss level within pre-set parameters while also maximising work rates. Because the cleaning pan capacity is constantly monitored and adjustment is automatic, potential overload situations are identified before they occur, so losses are minimised.
“Previously, getting the best from the combine relied on judgement and guessing what was happening inside, but IDEALharvest provides a real-time visual illustration of the whole process on the screen,” Ben explained. “In effect, I can see exactly what is happening inside at all times, so if issues occur I can see why, and when things are going well I can improve them further. I use an iPad to monitor IDEALharvest which leaves the main Varioterminal free for GPS steering and monitoring combine performance.
“With many years of experience operating combines on a large acreage I rate my ability to get the best from the machine highly. In a good crop where conditions are constant, when I set the combine up myself and switch off the automation, I can match the results.
“But conditions change frequently within fields and during each day, and this year’s crops were particularly variable where ground conditions remained wet over winter. Operating everything manually my natural reaction is to increase travel speed where the crop is thin and slow down again as it becomes thicker. IDEALharvest does this too, but it also adjusts the threshing and cleaning systems for optimal results at the same time and continues doing it throughout the day. An operator couldn’t maintain that performance.”
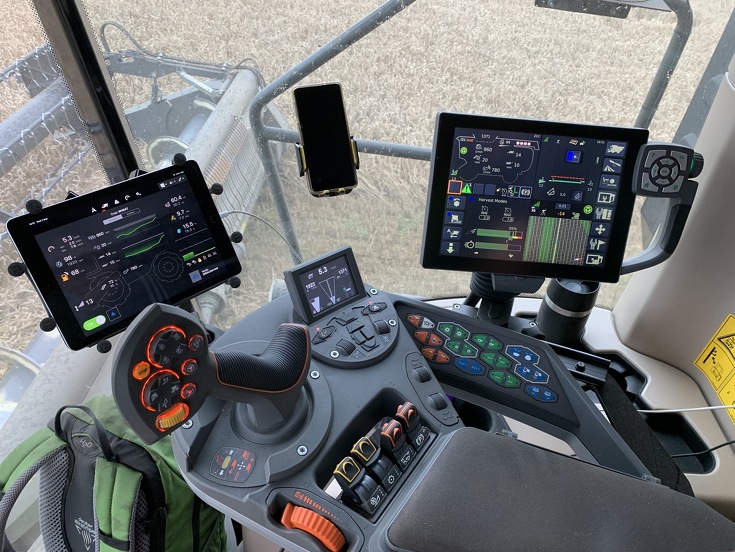
Ben’s combine is equipped with Fendt’s IDEALharvest which automatically adjusts the harvesting settings, and he says there is no way he could match its performance in patchy crops which featured this year.
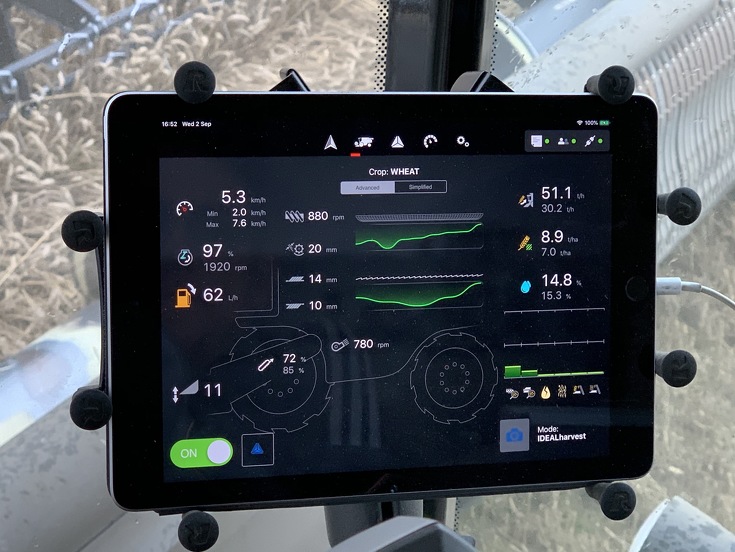
IDEALharvest is displayed and controlled through an iPad. Ben describes it as having ‘eyes inside the machine’.
The second Ideal 8T doesn’t have IDEALharvest, but it is equipped with Fendt’s Machine to Machine communication feature. This allows settings and data including A-B guidance lines to be shared. Once Ben has identified optimum harvesting settings they can be sent to the other combine for acceptance by operator Alex Robinson to use as a starting point, then he can tweak them as required. Both operators use the Ideals’ HarvestPlus function which allows maximum threshing load and travel speeds to be set for the combine to try to maintain, but Alex said that working side by side in variable crops highlights the benefits of IDEALharvest, as his combine struggles to match Ben’s work rate and grain sample. “The automation definitely increases productivity,” he confirmed.
Other operator aids which are popular with the users include automatic raising of the header when the main control joystick is pulled back quickly. “It’s especially useful when working around the field edges,” said Ben. “If you suddenly notice an obstruction the natural reaction is to pull the stick back quickly to stop the machine, and when you do that on the Ideal the table lifts too. As soon as the stick is pushed forward again the table returns to its previous working position, so it’s a useful feature. There is also hydraulic header pitch adjustment which allows the table to be tilted forwards or back up to six degrees, to suit the crop type and conditions.”
The second Ideal 8T doesn’t have IDEALharvest, but it is equipped with Fendt’s Machine to Machine communication feature. This allows settings and data including A-B guidance lines to be shared. Once Ben has identified optimum harvesting settings they can be sent to the other combine for acceptance by operator Alex Robinson to use as a starting point, then he can tweak them as required. Both operators use the Ideals’ HarvestPlus function which allows maximum threshing load and travel speeds to be set for the combine to try to maintain, but Alex said that working side by side in variable crops highlights the benefits of IDEALharvest, as his combine struggles to match Ben’s work rate and grain sample. “The automation definitely increases productivity,” he confirmed.
Other operator aids which are popular with the users include automatic raising of the header when the main control joystick is pulled back quickly. “It’s especially useful when working around the field edges,” said Ben. “If you suddenly notice an obstruction the natural reaction is to pull the stick back quickly to stop the machine, and when you do that on the Ideal the table lifts too. As soon as the stick is pushed forward again the table returns to its previous working position, so it’s a useful feature. There is also hydraulic header pitch adjustment which allows the table to be tilted forwards or back up to six degrees, to suit the crop type and conditions.”
Two Fendt Ideal 8T combines with 10.5m SuperFlow headers have completed their second harvest for Lincolnshire Field Products.
Simple record keeping
VarioDoc Pro is also used by the farm, simplifying the sharing of task and management data between the combines and farm office. Before entering a field or cutting block, details of fields to be harvested are sent to the combines from the farm management system (FMS). As the combines enter the field the location is recognised, and boundary and guidance lines are automatically loaded. Yields and moisture data are recorded and when the field is completed the information is automatically sent and loaded into the FMS back at the office. It’s fully automated and seamless.
Getting it right
Before this harvest all Ideal combines were updated to solve issues noted previously at LFP and elsewhere. “It’s a completely different machine now,” stressed Ben. “We had several teething issues last year, including with IDEALharvest which meant that for much of the time I set everything up manually. But another problem resulted from our dense straw. We have some very fertile soils with a high moisture content and, as a result, our straw yields can be exceptionally high. On a few occasions this restricted the crop flow from the header, which meant we struggled to keep the threshing system full. The modifications were successful and there were no similar issues this harvest. It eats anything.”
The two Ideal 8Ts achieved spot rates in wheat of 60–65 tonnes per hour, and an average of 45-plus tonnes per hour, despite patchy crops due to the unfavourable winter and spring weather. Straw quality is described as equivalent to a straw walker combine, and the grain sample is excellent with minimal grain damage. Losses are said to be negligible. “This is the sort of performance we hoped for from this size combine,” added Ben. “Achieving maximum grain quality is essential as we produce seed, we wanted higher work rates and keeping the straw intact is also important. The Dual Helix rotors provide a huge threshing and separation area which means the crop isn’t battered and squeezed. Instead the straw is handled gently and fluffed up, leaving it perfect for baling.”
Unloading rates up to 210 litres per second mean the large 12,500-litre grain tanks are emptied quickly.
The rate can be adjusted in five stages reducing the risk of spillage while topping off trailers.
Saving Fuel
Despite achieving higher work rates than the farm’s previous combines, the Ideals use significantly less fuel. Each combine consumes approximately 800 litres during a typical working day, representing a saving of 30 litres per hour or 400 litres per day compared to the combines replaced, and a full tank provides enough fuel for two days’ work.
“We are very pleased with our decision to invest in the Ideal 8Ts,” confirmed Paul. “Back-up from Clive Barber and the rest of the Chandlers’ team remains second to none, and work carried out by Fendt to rectify issues we experienced last year has been successful. We wanted higher output, improved fuel economy, an excellent sample and best possible straw quality, and all these requirements are being met.”